A palavra ‘Blisk’ é uma união de ‘Bladed e Disk’. É um componente de peça única composto por um anel de pás de aerofólio dispostas em torno de um cubo central onde o Blisk gera movimento rotacional a partir da força do ar que sopra através de um motor aeronáutico. Tradicionalmente, os Blisks só foram encontrados em motores aeronáuticos militares, por exemplo, nos estágios de combustão de baixa pressão do EJ200 Euro Fighter e do F35 Lighting II – Joint Strike Fighter, devido à complexidade de fabricação e aos custos associados.
Otimizações do percurso da ferramenta para aumentar a produtividade do cliente
Os avanços no CAM e as máquinas-ferramentas cada vez mais capazes permitiram que a tecnologia Blisk se tornasse mais prontamente disponível para uso em motores aeronáuticos comerciais.
A equipe Global Consulting Delivery (GCD) da Autodesk foi contratada por uma empresa de fabricação aeroespacial para fornecer melhorias no desenvolvimento de processos em sua produção Blisk. O objetivo do cliente era simples; reduzir custos reduzindo o tempo do ciclo de usinagem. A restrição era que o cliente não desejava que o conjunto de ferramentas de corte fosse alterado, especialmente para acabamento.
A razão disto é que os componentes aeroespaciais e os seus processos de fabricação definidos são rigorosamente controlados; quaisquer alterações devem passar por longos processos de validação. Manter a consistência do cortador evita que esta revalidação seja necessária e, assim, as melhorias do processo possam ser implementadas imediatamente.
Dadas as restrições impostas, o benefício global foi limitado. No entanto, mesmo com essas limitações, ao usar estratégias de usinagem poderosas no Fusion 360 com PowerMill, o tempo do ciclo de usinagem do cliente foi reduzido em 40% e os objetivos do projeto foram alcançados com sucesso. Durante a revisão de encerramento do projecto, a equipe Autodesk questionou-se sobre o que poderia ser alcançado sem tais limitações; até onde o software e o hardware poderiam ser levados e até que ponto os tempos de ciclo de usinagem poderiam ser reduzidos?
Além dos limites
Detalhes do estudo de caso
- Blisk de 800 mm de diâmetro
- MaterialTi-64
- 31 lâminas: 120 mm de altura e 84 mm de comprimento de corda
- Boleto sólido pré-tornado
- Tempo de ciclo de referência nas instalações da Autodesk: 135 horas
- Custo atual do cortador: £ 2.200
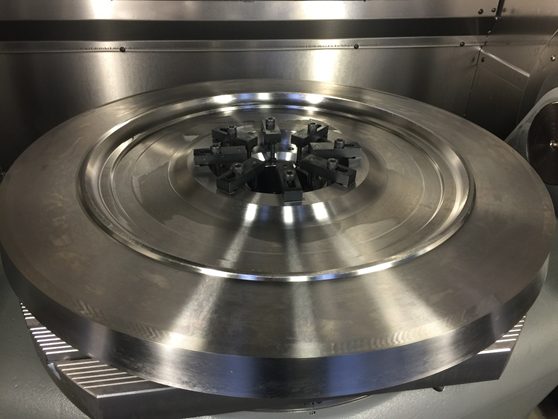
A intenção da Autodesk era reduzir enormemente o tempo do ciclo de usinagem. Para conseguir isso, todos os aspectos do processo de usinagem foram considerados; não apenas a estratégia de corte, mas também a máquina-ferramenta, acessórios, fresas e suportes de fresas.
Os percursos de aerofólio Blisk geralmente consistem em muitos passes rasos de desbaste, semi acabamento e acabamento utilizando fresas de ponta esférica. Isto apresenta alguns desafios. Os aerofólios são normalmente altos e finos e por isso se movem e vibram durante o ciclo de usinagem, o que causa problemas. Em particular, o movimento e a carga na fresa mudam constantemente. Isso resulta em um efeito constante de empurrar/puxar o material e o aerofólio que estão sendo usinados. Essas forças imprevisíveis resultam em condições materiais inconsistentes ou em marcas de usinagem deixadas na superfície do aerofólio. A combinação e abordagem do percurso de ferramenta utilizada era completamente diferente da abordagem convencional, que tradicionalmente compreenderia muitos passos de corte superficiais, mas rápidos, e seria limitada aos tipos de fresas esféricas. Esta abordagem foi modificada para usar uma operação de ranhura para cortar cada perfil do aerofólio, removendo a quantidade máxima de material no menor tempo possível para produzir uma forma quase final. Fresas de desbaste e acabamento tipo barril foram então usadas para finalizar a peça. A forma em barril permite obter um maior passo lateral e reduzir os tempos de ciclo. Normalmente, esses tipos de fresas podem ser difíceis de programar e controlar devido a uma combinação do formato da fresa de raio grande e ao desejo de minimizar o movimento do eixo da ferramenta, evitando colisões do suporte com a peça. Os algoritmos de suavização e controle do eixo da ferramenta Blade, Blisk and Impeller (BBI) dedicados do PowerMill, juntamente com a prevenção e verificação automática de colisões, tornaram a experiência de programação mais rápida e fácil, com poucas iterações e o mínimo de edição pós-cálculo necessária.
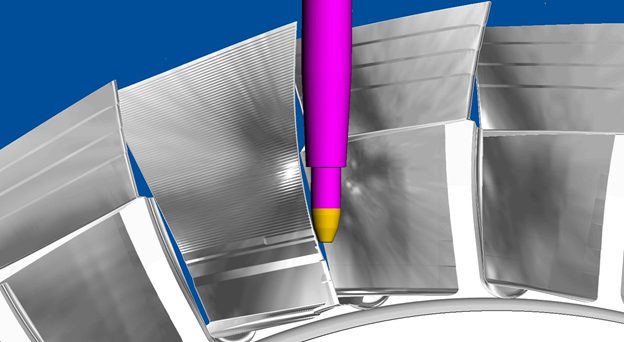
A chave para o sucesso da estratégia de usinagem foi a disponibilidade e a variedade de equipamentos disponíveis internamente no centro de tecnologia da Autodesk no Reino Unido , onde o acesso a uma máquina CNC multieixos comumente usada na indústria aeroespacial estava disponível para o desenvolvimento de processos.
Também vital para o sucesso foi a parceria estratégica da GCD com uma empresa especializada em ferramentas de corte cuja especialidade é projetar e fabricar fresas com tolerâncias extremamente restritas e fabricá-las para cada processo específico. Eles produziram fresas com tamanho, formato e tolerância exatos, incluindo os suportes de fresa, e forneceram a experiência necessária para aprimorar os parâmetros de corte do processo.
Essas fresas otimizadas permitiram que as estratégias do percurso da ferramenta fossem totalmente otimizadas, maximizando as velocidades de corte, avanços, profundidades e larguras de corte e características de potência e estabilidade da máquina-ferramenta. O titânio é um material muito caro e os Blisks exigem um enorme investimento em tempo e maquinário para serem produzidos, tornando-os itens altamente valiosos e caros de produzir. Para garantir um controle rigoroso sobre a qualidade da peça, foram realizadas medições durante todo o ciclo de usinagem usando o Fusion 360 com PowerINSPECT . A verificação na máquina (OMV) é um processo de uso de uma sonda de toque no fuso da máquina para fazer medições do componente. Medir o Blisk na máquina-ferramenta desta forma verificou a quantidade correta de remoção de material, além de garantir que os aerofólios estavam estáveis e não deformados. Isto proporcionou validação e garantia de que essas peças caras seriam precisas e corretas quando o ciclo de usinagem fosse concluído. A inspeção final foi realizada no departamento de controle de qualidade do centro de tecnologia da Autodesk no Reino Unido, usando uma Máquina de Medição por Coordenadas (CMM) e equipamento de digitalização óptica 3D.
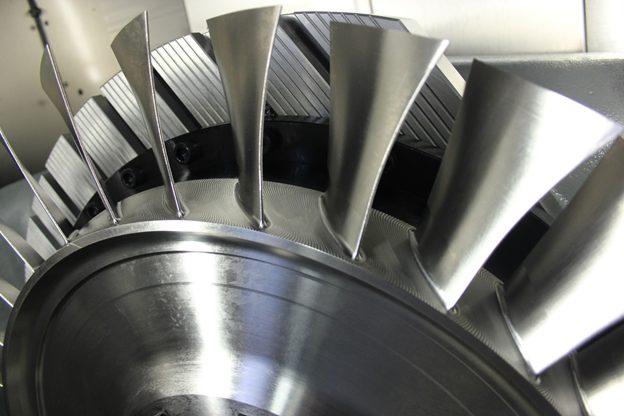
Detalhes de conclusão do estudo de caso
- Custo do cortador: £ 1.217
- Total de cortadores usados: 18
- Tolerância alcançada: ~0,01 mm
- Tempo de ciclo alcançado: 35 horas
Economia em resumo
A economia total no tempo de ciclo foi de 135 horas, reduzida para 35 horas, o que equivale a uma economia de 74%. Incrivelmente, o custo do ferramental também foi reduzido em 45%. Tudo isto permitiria ao fabricante mudar a forma como vê estes produtos e potencialmente perturbar o seu portfólio de produtos.
Para obter mais informações sobre como a equipe de entrega de consultoria global da Autodesk pode ajudá-lo com seus problemas de fabricação, entre em contato com a equipe da CAMSERV SOLUTIONS.
Originalmente traduzido de: https://blogs.autodesk.com/advanced-manufacturing/2021/11/10/blisk-machining-reduced-through-innovative-methods/